
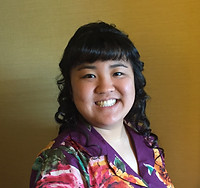
Amy Chow

Morgan Oldfield
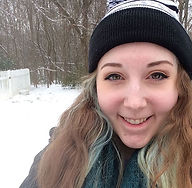
Karis Campbell
In our senior design class, Morgan Oldfield (bioengineering), Karis Campbell (bioengineering) and I have formed a team focused on creating affordable prosthetic legs for amputees who live in impoverished communities. Our project, the EcoLeg, is a 3D printed prosthetic leg that is durable and made of Eco-friendly materials.
For the first three months, we learned the basics of building a business from the ground up and have created a quality manual for our "company" that includes important documentation such as company processes, design controls, ISO and FDA regulations, financials and GAP analysis.
One of the biggest challenges of this process was identifying the federal regulations that are important to our product and business. We sought help from professors regarding our search and asked a lot of questions about navigating different government websites. I also learned that the company organization doesn't just flow in one direction. There can be somewhat of a hierarchy. However, there also needs to be connections between each person and department to indicate the communication and teamwork that needs to occur in order to make the business successful.
​
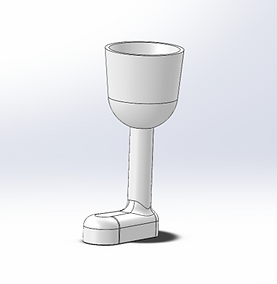

For the last few months, my team and I have been focused on developing prototypes of our product. Initially, we planned on creating an entire prosthetic leg with interlocking parts. Each piece would slide together along a track for easy assembly. This would allow the user to replace only the damaged pieces rather than the entire prosthetic. However, after doing more research, we realized that what we had hoped to accomplish with the current design wasn't realistic and that creating an entire prosthetic leg wasn't very cost effective.
Based on customer discovery, we found that the most common problems with prosthetic legs involve the fit of the socket and not the prosthetic leg itself. Swelling and constant residual limb changes cause the socket to become too tight and uncomfortable. Because of this, we decided to shift our focus to developing a replaceable socket. The socket would still be made of recycled materials, but would also come with a padded inner lining and buckle at the top to provide more comfort for the wearer.
Unfortunately, we were unable to make a physical prototype due to the Covid-19 pandemic. However, we did conduct a force analysis to determine the feasibility of the design. The example below (right) was created using Solidworks Simulation and shows the stress and strain for a 200 lb downward force. Currently, the weakest point of the model is at the base. New models are under development to combat this and further testing will be done to evaluate the performance over a long period of time.


The biggest takeaways from this project was definitely the importance of doing your research and to be realistic when it comes to figuring out what problems to focus on. At the beginning, we made a lot of wrong assumptions about our market and customer base and didn't do enough research to realize that we weren't focusing on solving the right problems. As a result, we lost a significant amount of time redoing our business model and creating new prototypes from scratch. It's hard to have to choose the problems to solve when you really just want to solve everything. However, there are a lot of trade offs in engineering and you need to focus on the most important problems first.
​
Feel free to view our most recent company documents below. The Technical Report goes into depth about our new product and prototype. The Business Model Report includes all updates on company processes including our new value proposition, market analysis, and financials.